Defect Flagging Equipment & Materials
Safety and accuracy aren’t a trade-off in our books. We distribute Novation defect flagging equipment and materials because of their proven defect recording and tracking performance. Novation is a world-leading, cost-effective solution that automatically marks and tracks defects while minimizing accidents and waste. Since 2002, Novation has been trusted by printers and converters to help them enhance operations.
Novation AF3 WebFlagger
For webs moving up to 4,000 fpm, the AF3 WebFlagger safely and accurately flags defects and connects with all inspection systems and upstream locations.
Novation ScrapTracker
Log a wide range of defective material causes and amounts with process parameters to report efficiency more easily. Able to operate independently or integrated with defect tracking, ScrapTracker data files (“roll maps”) aggregates the information you need to automate roll reporting.
Novation RollCode System
Integrate ScrapTracker’s roll maps with our RollCode system to map your data and automatically stop your machines at each flagged location. Quality control departments can analyze valuable data to implement process improvements and scrap reduction programs.
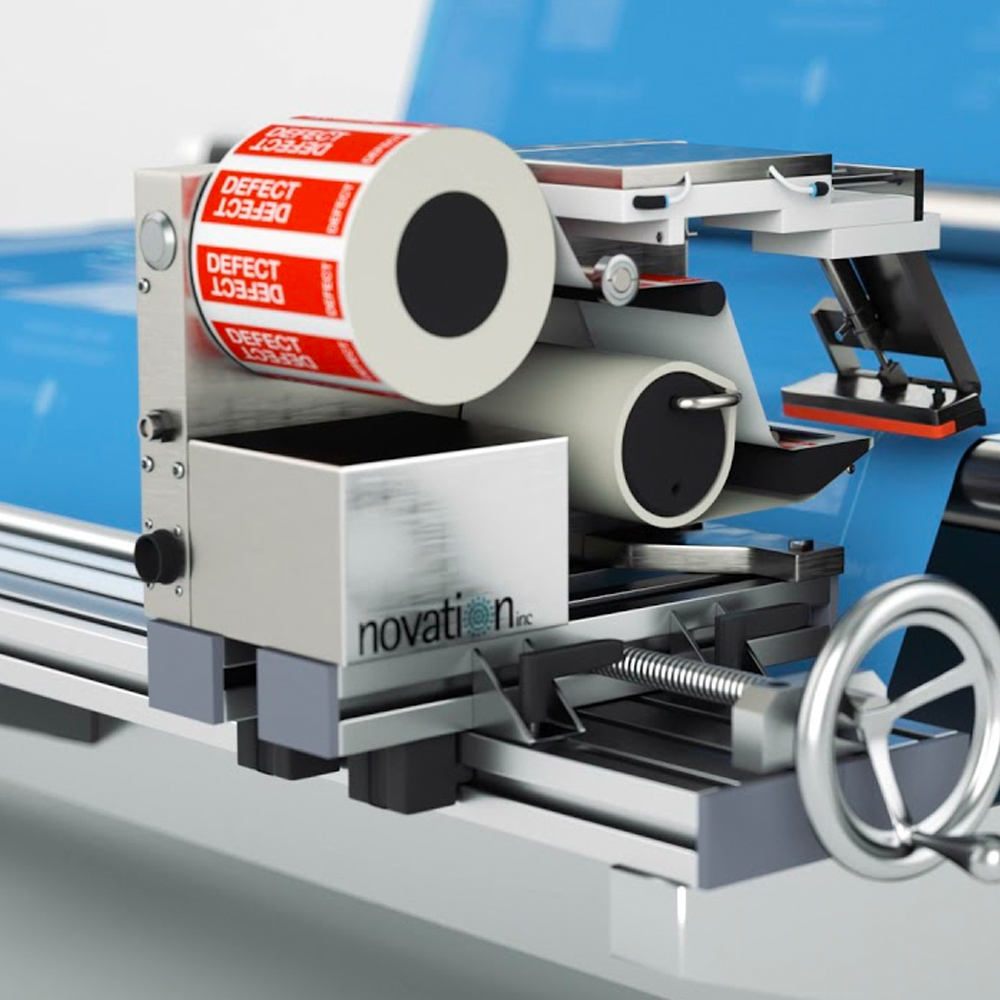
Provident Defect Flagging & Materials
Why Choose Novation Defect Marking & Automation?
The unique needs of the printing and converting industries require highly specialized defect flagging equipment that can exceed expectations.
Novation solutions offer a comprehensive range of solutions, including the Novation AF3 WebFlagger, ScrapTracker, and RollCode System, which can integrate for end-to-end actionable reporting.